Mercedes: Besuch in Wörth
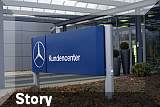
Ein Besuch in Wörth
Eine Werksbesichtigung
Vor dem Gang durch die Produktion bekomme ich eine Einweisung in die neue militärische Fahrzeuggeneration Unimog U 4000 und den Mercedes-Benz S 2000. Beide geländegängigen Fahrzeuge pflügen durch das Gelände, als wären Steigungen von bis zu 45 Prozent keine Hindernisse für sie.
Martin Reis (43) Testfahrer auf dem Unimog: „Natürlich braucht man Erfahrung, um dieses schwierige Gelände zu meistern.“ Als Beifahrer bekommt man in der Magengegend ein Gefühl von Seekrankheit. Schnee, Matsch, Kies und Dreck sind der ideale Untergrund für diese Fahrzeuge. Beide Lkw sind natürlich luftverlastbar. Den Unimog gibt es in den Ausführungen U 3000, U 4000 sowie U 5000. Das Allradfahrzeug leistet bis zu 218 PS.
Der S 2000 ist noch ein Prototyp. Er basiert auf einem Actros-Lkw und leistet zwischen 280 bis 326 PS. Der S 2000 wird vermutlich ab 2008 in die Serienfertigung gehen. Weitere Militärfahrzeuge von Mercedes-Benz sind die G-Klasse, dem Soldaten besser als Wolf bekannt (mit 156 PS, CDI-Motor), Sprinter, Vario sowie modifizierte Fahrzeuge der Atego- und Actros-Klasse, die Nutzlasten zwischen drei und mehr als 22 Tonnen bewegen. Die Motorisierung reicht von 177 bis 603 PS (Panzertransporter bis 250 Tonnen).
Selbstabholung mit Werksbesichtigung
Drei von vier Kunden holen in Wörth ihren Mercedes-Benz selbst ab. Sie sparen sich die Überführungskosten und erleben noch eine faszinierende Werksführung. Etwa 25.000 Besucher werden jährlich durch das Werk geführt. Zirka 66 Stunden dauert es, bis ein Nutzfahrzeug – von dem ersten Fügen der Bleche, über Schweißen, Lackieren bis zur Endmontage – an den Kunden übergeben werden kann. Gearbeitet wird im Zwei- oder Drei-Schichtbetrieb.
Die Zulieferer fertigen ihre Produkte, meist zwischen zwei und drei Lkw-Fahrstunden, im Umkreis von Wörth am Rhein oder auch direkt auf dem Werksgelände. Nur so kann sichergestellt werden, dass die Teile pünktlich zwischen 30 bis 40 Minuten vor dem Einbau angeliefert werden. „Just in Time“ heißt dieses Prinzip. Für viele Teile benötigt man daher keine teure Lagerhaltung.
Wie von Geisterhand bewegt, gleiten die Fahrerlosen Transport Fahrzeuge (FTF) von Station zu Station. Wir gehen durch die Abteilung „Fertigung Vorbau“. Hier sind nur wenige Mitarbeiter direkt in der Produktion beschäftigt. Die Teile werden automatisch Millimeter genau gefügt und von den FTF zur Punktschweißung transportiert. Autoentwickler sind da wenig „tolerant“. Auch im Bereich Nutzfahrzeuge (NFZ) wird ein enges Spaltmaß gefordert. Etwa 3.900 Schweißpunkte werden allein am Fahrerhaus gesetzt.
Für jeden Kunden die richtige Farbe parat
Die Lackierei kann natürlich nicht betreten werden. Die Information bekommt der Besucher über einen anschaulichen Film. Von der Phospatierung geht es zur Kathodischen Elektrotauchlackierung und weiter zur Nahtabdichtung. Nach Hydrofüller, Decklack und Hohlraumkonservierung inklusive Trocknung verlässt die Kabine die Lackierei.
Und immer wieder Qualitätskontrolle. Mit einem 3D-Taster werden regelmäßig die Fahrzeugkabinen überprüft. Funktionsmaße, Effektivmaße, Anschraubpunkte: Alle Lkw müssen wie aus einem Guss sein. Etwa 10 bis 20 Karossen durchlaufen täglich diese Stelle.
Handarbeit in der Sektion Innenausbau
In der Baugruppenvormontage sind etwa 450 Mitarbeiter beschäftigt. Nach präzise 2:30 Minuten müssen bestimmte Arbeiten erledigt sein. Takt nennt das der Fachmann. Dann übernimmt ein anderes Team die Karosse. Die digitale Anzeige im Werk gibt die Information: 386 Kabinen werden heute gefertigt. Die Halle ist hell und freundlich, und es herrscht eine angenehme Temperatur. Es wird ruhig und zielstrebig, aber ohne Hektik gearbeitet. Die Mitarbeiter tragen Latzhosen und T-Shirts. Es gibt keine Uniform.
Rahmenmontage
Schritt für Schritt werden die Lkw komplettiert. In der Rahmenmontage arbeiten etwa 2.000 Mitarbeiter. Die Bandlänge beträgt 440 Meter. 6,5 bis 8,75 Stunden beträgt hier die Durchlaufzeit. Motoren und Getriebe sind etwa 1,5 Tage vor dem Einbau auf dem Werksgelände. Die „Hochzeit“ dauert exakt vier Minuten. So nennen die Fahrzeugbauer es, wenn Fahrerhaus und Fahrgestell montiert werden.
Der Motor wird gestartet. Das erste Mal in diesem Autoleben. Und viele Tausende Mal werden folgen. Die letzten Meter legt der Lkw mit eigener Kraft zurück. Der Wagen fährt auf einen Rollenstand. Es ist ein 815: Ein Fahrzeug mit 8 Tonnen und 150 PS. Der Testfahrer lässt den Lkw eine bestimmte Zeit bei etwa 35 Kilometer pro Stunden „rollen“ und beschleunigt dann auf 80 Stundenkilometer.
Test bestanden. Etwa 200.000 bis 300.000 Kilometer legt ein Lkw pro Jahr zurück. Zirka vier bis fünf Jahre rollen die Fahrzeuge für eine Spedition – bleiben in erster Hand. Immer mehr Lkw werden mit BlueTec-Technologie geordert. Für die Auslieferung an deutsche Kunden ist es fast jeder zweite Lkw. Die Fahrzeuge erfüllen schon heute die strenge Euro-5-Norm. ♦